Система Just-in-time
Выполнили:
541-Ук
Возникновение Just-in-time
В конце 1920-х годов Кииширо Тойода (сын основателя компании Toyota – Сакиши Тойда) побывал в США, после чего загорелся идеей разработать японский автомобиль. Но спрос на машины в Японии был невелик а также в стране как и сейчас была проблема ограниченных ресурсов и свободных площадей для хранения запасов, поэтому Тойода не мог, как Генри Форд сделать автомобиль конкурентоспособным при помощи массового производства, тогда он решил производить только то, что нужно, когда нужно и сколько нужно.
Цель компании Toyota состояла в следующем: сохранить эффективность поточного производства Ford, но сделать его возможным в условиях ограниченных ресурсов и ограниченного спроса.
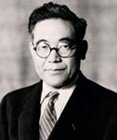
Кииширо Тойода
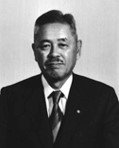
Тайчи Оно
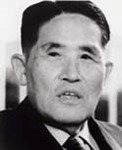
Шигео Шинго
Система JIT в Японии и начала использоваться в конце 50-х годов. Потребовалось около двадцати лет, чтобы технология JIТ перешла в западную промышленность, и около десяти лет, чтобы реализовать концепцию в целом.
Рождение и развитие системы JIТ именно в Япони было естественным, поскольку она попала на благодатную почву нации, которую характеризуют фанатичная дисциплинированность и безупречная аккуратность.
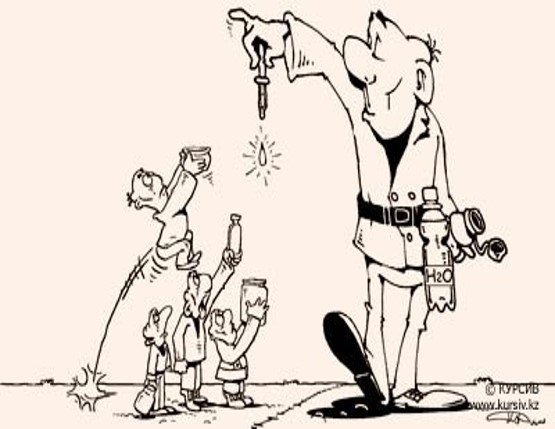
-
Система JIТ эффективна только при использовании TQM, так как в ее основе применительно, например, к производству - 'правильная' спецификация деталей и готового продукта при 'правильном' их количестве, в 'правильное' время, без брака.
-
Все неиспользуемые какое-то время запасы являются непроизводительными расходами, которые возрастают в зависимости от времени хранения неиспользуемых запасов и их объема.
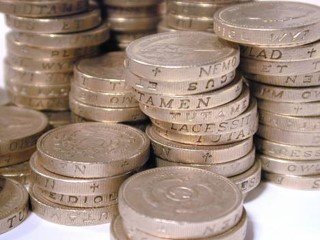
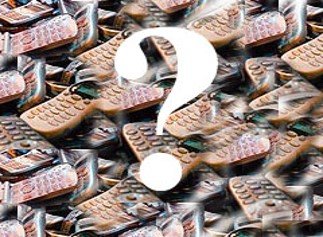
Для применения системы JIТ необходимо
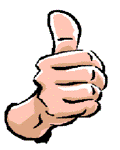
-
хорошее качество, обеспечиваемое проверкой процесса;
-
профилактическое техобслуживание;
-
сокращение процесса производства путем сокращения времени подготовки;
-
полная ответственность как внешних, так и внутренних поставщиков последующих операций процесса, которые должны обеспечивать высокое качество выхода процесса.
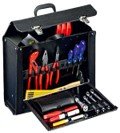
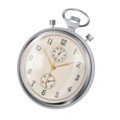
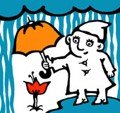
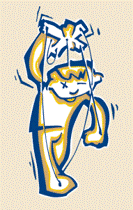
Один из необходимых элементов системы JIT – самоконтроль.
JIT – pull system
В отличие от MRP (планирование требуемых материалов) система JIТ является 'вытягивающей' ( pull system), т.е. системой с такой организацией процесса, когда последующая стадия производства 'вытягивает' все необходимое с предыдущей в нужный момент времени. В этом случае выход конечной стадии основан на запросах потребителя или соответствует графику производства.
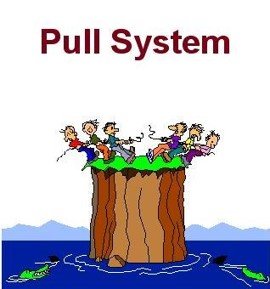
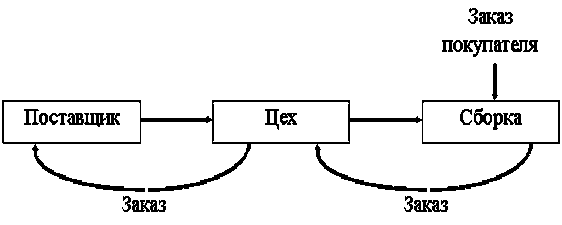
JIT и MRP
-
Эти две системы, которые на первый взгляд могут показаться противодействующими, выгодно соединяются для одного и того же производства. Например, MRP (push-система) успешно применяется при планировании производства, а JIТ (pull-система) очень удобна для управления им или компанией, работающей в условиях TQM.
-
Обе эти системы опираются на принцип:
-
что;
-
сколько;
-
когда.
Цели применения системы JIT в компании:
-
постоянное улучшение качества и надежности процесса;
-
минимизация стоимости брака (стоимость изготовления и последующая переработка брака, увеличение изготавливаемой качественной продукции);
-
минимизация площадей, необходимых для организации производства;
-
минимизация времени от момента получения заказа до его выполнения.
Действие системы JIТ можно описать как:
-
серию (ряд) действующих положений, позволяющих систематически распознавать проблемы управления с позиции концепции ЛТ;
-
серию основных инструментов управления, позволяющих отслеживать систему JIТ.
-
Примером инструментов управления являются:
-
система JIDOHKA, т. е. система автоматической остановки всей линии при обнаружении недостатков;
-
система AN DON, т. е. система управления, в которой путем световой сигнализации можно отслеживать ход выполнения производственного процесса и при необходимости вмешиваться в него.
система JIDOHKA
-
Конечная цель системы JIDOHKA - предотвратить любой вид брака. Поэтому при возникновении любой проблемы лучше остановить линию (машину), чем продолжать производство. Остановка может выполняться автоматически или вручную. Действия, связанные с применением системы JIDOHKA, имеют следующую последовательность:
-
остановка линии;
-
контроль оборудования и контакт оператора с лицом, отвечающим за линию;
-
совместная проверка недостатка и выявление причин его появления;
-
передача информации по линии;
-
принятие необходимых мер и запуск линии.
Как нетрудно заметить, применение системы JIDOHKA временно снижает производительность, т. е. количество изготовленных деталей. Однако время восстановления работы линии, обычно сравнительно